Works safely in additive manufacturing with Dupuy industrial vacuum cleaners.
Additive manufacturing has revolutionized the field of prototyping.
The technology of “Powder bed fusion”
When the printer finishes scanning and melting the dust of the level, the worktop will be lowered to allow the deposit of a new level of dust in the same amount as the previous one.
This step-by-step procedure will be carried out until the complete realization of the artifact.
There are several techniques to heat and melt the powder, below the most used:
- Thermal fusion
- Laser fusion
- Electron beam fusion
- Fusion with agents and energy
Where DUPUY Industrial vacuum cleaners intervene
- Cross contamination between different production cycles, resulting in loss of product quality and integrity;
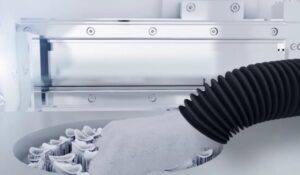
- Hazards to the health of employees, fine dust can be inhaled with consequent health problems while metallic dust could damage the skin;
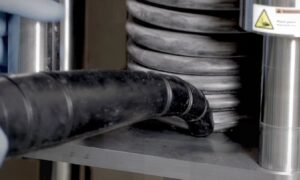
- Risk of explosion, where the processing is carried out with conductive metallic or plastic powders, the latter must be treated after aspiration;
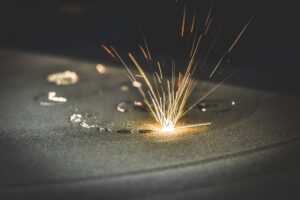
- The creation of a dirty environment, keeping the working area clean and healthy;
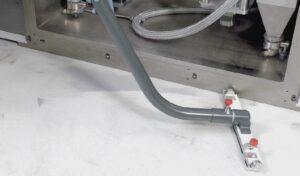
Kind of powders
In order to choose the right vacuum cleaner, it is necessary to analyse the powders used during the process. The values to be taken in consideration are the following:
- Morphology
- Density
- Composition
- Smoothness
- Thermal properties
- Combustibility
- Conductivity
The values of conductivity and combustibility are the most important in the choice of the type of aspirator.
In the case of non-conductive combustible dust, the ideal vacuum cleaner will be equipped with antistatic filter, earth grounding and brushless motor, certified ATEX zone 22 for cleaning in total safety.
With combustible and conductive powders DUPUY has instead designed a special version with inertizing bath inside the container.
Our vacuum solution
The W2 certified ATEX zone 22 (Ex II 3D tc IIIB 135 and C X Dc) IP55 is the industrial vacuum cleaner suitable for the collection of non-conductive combustible plastic powders:
- 1 powerful brushless motor
- Large antistatic polyester star filter cat. “M”
- Additional Hepa H14 absolute filter available (optional)
- Stainless steel container
- Earth Grounding
- Compact size for the best ergonomics
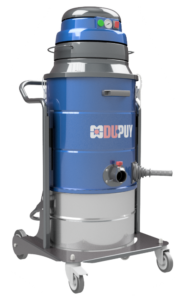
Container with inertizing oil bath
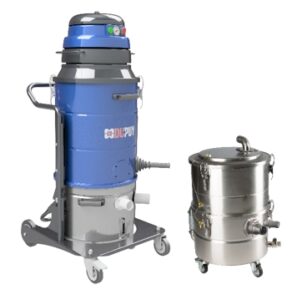
It is also available the filter separator with inertizing bath to connect to other models of vacuum cleaners with larger capacity and power.
- Simple disposal of vacuum dust
- Simplified oil discharge
- 4 filtration stages
- Reusable oil
- Exchangeable container or filtering preseparator suitable for matching with any industrial vacuum cleaner